
iPowder™ navigation links below or to left:
About iPowder Systems
About E&G Associates
Our approach
iShear Rotary Split Cell
What is powder flow?
Workshops
Publications & presentations
Contacts
Contacts:
Questions, requests for equipment demonstration, or development requests should be directed to:
iPowder@evinsmill.com • Tel:615.591.7510 • Fax:240.524.8482
Downloads:
Upcoming flow course registration flyer: Registration flyer
What is powder flow? PowderNote-PN1
In-house seminar (request quotation): Flow Seminar
Request an on-site equipment demonstration: Demo
Download information on the iShear split-cell rotary shear tester: iShear Rotary Shear Tester
|
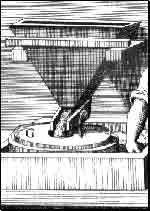
|
|
|
About iPowder Systems
Withover over two decades of experience in resolving problems faced by our clients, E&G Associates has developed significant and unique expertise in the application of powder characterization methods to the solution of processing and product development challenges. While often commercial instrumentation has been utilized for more routine measurements, this work has often necessitated the development of state-of-the-art characterization techniques for particulate systems, especially in the areas of surface chemical, rheological and mechanical property determination.
At the behest of our clients, this led in a natural way to the inception of iPowder Systems and the development and commercialization of a state-of-the-art powder shear cell to assess powder friction and cohesion properties, iShear™. The iShear™ tester has been incorporated into development work of several clients, including in-process manufacturing release specifications for filling operations of one client and a joint CRDA with the FDA of another. Similar instruments are under design for compaction, IGC, caking, and granulation studies.
top |
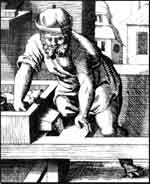
|
|
|
About E&G Associates
iPowder Systems is wholly owned by E&G Associates, and serves as a vehicle for instrumentation development for mechanical property measurements of powders as well as commercial sales. For more information about E&G Associates and its founder, please click on the following link to be redirected:
E&G Associates
top | 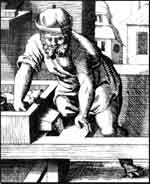
|
|
|
Our approach
Powder characterization in not a new realm of study, yet many of its principles have been slow to seep into industrial processing. (See e.g. "Particle Technology - The Legacy of Neglect in the US”, Chemical Engineering Progress, 1994. Ennis et al.) In fact, the recent rate of re-"discovery" of new phemonena such as segregation and powder flowability among engineers and physicists is surprising. Yet powder technology has a rich tradition dating back to Reynolds, Faraday, Coloumb, and Mohr. In the case of powder mechanics, one of the original papers about stress transmission hails from geotechnical engineering over a 100 years ago (Janssen, 1895). But many do not appreciate the direct applications of this work to e.g. tabletting.
With the growth in process measurements and especially initiatives such as Process Analytical Technology (PAT/FDA), it is important that sound engineering principles drawing on powder technology understanding not be neglected in the development of instrumenation. Within the reference of powder research and particle characterization, Professor Roland Clift, O.B.E. (Univ. of Surrey, UK) in a plenary lecture to the Particle Technolgy Forum of AIChE coined the phrase - "powder rituals." Essentially, he wished to emphasize that rather than rely on rituals in powder testing which measure more the interaction between test equipment and the powder, we should instead attempt as best we can to measure properties of the powder itself -- what we would define as material variables.
In order to lay a sound engineering foundation for powder processing, it is important the instrumentation measure these material properties, which in principle, are independent of the test apparatus itself, and that such intrumentation be traceable to international standards to allow validation. This is one of our mission statements - to develop sound engineering instruments, easy to use by operators, and validated against standards - and to dispel the notion that we must or should rely on "powder rituals."
top |
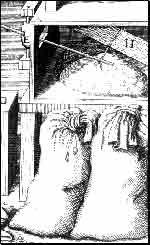
|
|
|
iShear™ Rotary Split Cell
Shear cells determine simple flow indices, which are measures of the forces required to initiate flow, defined as powder failure, based on measurements of cohesive strength, powder friction, and wall friction. This information is extremely useful for bin design, minimization of caking & segregation, and processes such as filling operations, roll pressing, tabletting, and encapsulation.
The iShear™ tester has been incorporated into development work of several clients, including for example, in-process manufacturing release specifications for filling operations of one client and a joint CRDA with the FDA of another.
Technical Specifications
-
An automated, rotary split-level shear tester used to characterize powder flowability, friction, and density relevant to material handling, segregation, caking, filling and feeding operations, particle/granule strength and compaction studies.
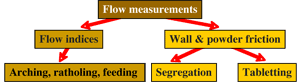
-
Measurements of powder flow index, internal powder friction, wall & die friction, bulk density, cohesive strength, and sample degradation versus compaction pressure.
-
Based on ASTM flow standards (Committee D18.25, D6682-01, D6128-97), and supplied with Bureau of Common Reference standard validation powder & yield loci, flow function, and flow index factory calibration receipt. Units are factory and site validated to within 5% of and traceable to BCR116 standard limestone powder.
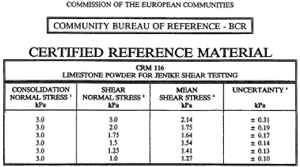
-
Reproducible measurements which are operator independent. Repeated consolidation shear measurements to within user specified standard deviations, and automated weight application.
-
Unlimited rotational shear and automated measurement allows complete and rapid flow characterization with a single sample, eliminating time consuming multiple measurements and samples as with traditional shear testers.
-
Standard equipment includes one shear cell (30 cm2 area, 45 cm3 volume), filling and consolidation accessories, wall friction coupons, validation powder, computer data acquisition unit & calibration/validation receipt. Appropriate safety & instrument protection interrupts.
-
Instrument controlled by a rugged CompactPCI ® data acquisition chassis with embedded Pentium processor, and user friendly point-and-click visual interface software running under Microsoft ® Windows XP operating system. Real time graphical display of all data, automatic flow index calculations, & report generation for Microsoft ® Excel.
-
Optional equipment includes: small pharmaceutical cell (3 cm2 area), density compressibility cell, automated consolidation bench, and an automated filling sieve. QC/manufacturing suitable manual version of shear tester also available.
-
One day training & installation. Optional material handling/compaction courses available on request.
Downloads:
In-house seminar (request quotation): Flow Seminar
Request an on-site equipment demonstration: Demo
Download information on the iShear split-cell rotary shear tester: iShear Rotary Shear Tester
top |
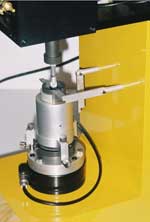
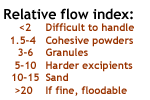
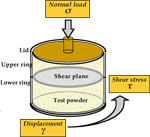
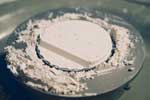
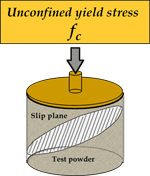
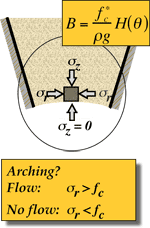
|
|
|
What is powder flow?
Powder flow effects solids dosage operations through material handling problems, segregation, tablet uniformity, and fill control. But when we say a powder has poor flowability, what exactly are we really saying?
Consider packing sand in a cup to to make a tower for a sand castle. It is immediately obvious that powders ARE NOT fluids, as the tower does not collapse. Bulk powders are solids. Powders can withstand pressure and stress without flowing (or more correctly, yielding), in contrast with most liquids.
If you pack the sand tighter, your tower will be stronger. Powders have a yield strength – just as a solid – which is a function of the history of compaction stress, as well as the current applied stress. This is a powder’s flow function. Bulk powders DO NOT have a viscosity, except possible in a fluidized state. Simply forget most of the things you were taught about fluids, since they rarely apply to powders.
Lets’ think about measurements. You may have used torque rheometers to measure fluid viscosity. Could this work for a powder? There are some key requirements for rheometers: the fluid must not slip on the torque surfaces, the strain-rate field must be defined and the material functions of fluid must be known. Otherwise, you cannot determine a viscosity, and can only measure torque for an ill-defined stress field. This is useful for telling you the torque required to shear this fluid IN THIS VESSEL and FOR THIS GEOMETRY. It tells you nothing about shear forces or flow in an actual process. Furthermore, attempting to extend traditional rheometric testing to bulk solids simply doesn’t work – since bulk powders are generally not fluids.
Bulk powders are solids. They exhibit anisotropic stress, elastic deformation & yield strength. They DO NOT flow in the sense of a fluid. They fail along slip planes, often don’t exhibit shear gradients, can slip on wall surfaces, and are less sensitive to strain rate. Their flow properties are measured by shear cells, developed from geotechnical soil mechanics.
Downloads:
What exactly is powder flowability? PowderNote-PN1
top |
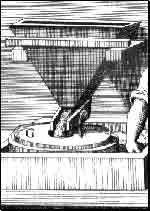
|
|
|
Workshops
Measuring Powder Flowability & Its Applications:
A Hands-On Design-Oriented Workshop
Nashville, TN • April 10-11, 2006
An intense 2-day powder flow & solids handling workshop conducted by E&G Associates, led by Dr.Bryan Ennis. This powder flow workshop should be of interest to those involved in powder and pharmaceutical processing issues for which powder flow properties are critical, including material transfer/handling, segregation, feeding and filling operations, encapsulation, roll pressing and tabletting. The course is equally of interest to those involved in formulations, bulk drug production, or quality control, who wish to engineer or control powder flow properties to minimize handling problems or improve product quality.
Get more detailed information on an upcoming workshop, please redirect to the following link:
Powder Flow Course
Upcoming flow course registration flyer: Registration flyer
top |
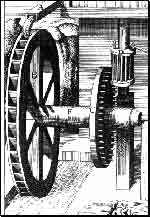
|
|
|
Publications and presentations
Please email us a request for any of the following presentations/publications:
-
Section 19: Solids-Solids Processing (Solids Handling), Perry's Chemical Engineers' Handbook, Sect.Ed. (Bryan Ennis), 8th ed., 2006. McGraw Hill (In preparation).
-
Section 20: Size Enlargement & Size Reduction, Perry's Chemical Engineers' Handbook, (Size Enlargment/Powder Mechanics, Ennis & Litster), 7th ed., 1994. McGraw Hill.
-
AAPS 2005 Annual Meeting:
Characterizing the Impact of Wall and Powder Friction on Tablet Uniformity as Measured by Shear Cell and Chemical Imaging
Ennis et al., Joint Paper with FDA. (Paper in prep.)
The Impact of Segregation on NIR Process Measurements
Ennis et al., Joint Paper with FDA. (Paper in prep.)
-
AAPS2004 Annual Meeting:
Characterizing the Impact of Flow Aids on the Flowability of Pharmaceutical Excipients by Automated Shear Cell
Ennis et al., Joint Paper with Cabot Corp. & & Tyco Health Care
-
Theory of Granulation: An Engineering Perspective, in Handbook of Pharmaceutical Granulation, 2nd Ed., B. Ennis, (Parikh ed.) Mercel-Dekker, 2005
-
The Science & Engineering of Granulation Processes, Litster & Ennis, Kluwer Academic, 2004
-
Proceedings of the First International Particle Tech. Forum, (B.Ennis, editor) AIChE, 1994
-
"Particle Technology - The Legacy of Neglect in the US”, Chemical Engineering Progress, Ennis et al., 1994.
Email request for more information:Paper request
top |
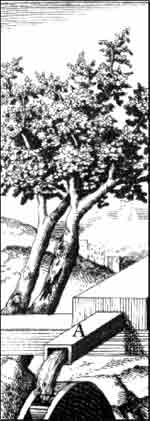 |